-
Applikationen
- Logistik
- Handhabung
- Montage
- Bearbeiten
- Schweissen
- Additiv Manufacturing
- Dosieren / kleben
- Messen + prüfen + testen
- Pick & Place
- Verpacken
- Palettieren
- Lackieren
- Abfüllen
- Disassambling
-
Branchen
- Pharma
- Medical
- Laborautomation
- Food & Beverage
- Metall & Holz
- Kunststoffe & Chemie
- Uhren
- Logistik
- Flugzeug & Raumfahrt
- Auto Zulieferer
- Whitegoods/Consumer
- Construction
- Bildung + Schulen
- Glas & Keramik
-
Komponenten
- Greifer
- Zuführungen
- Rundtische
- Sensoren
- Vision
- Kraftmomentensensoren
- Roboter
- Schutzäune
- Lichtschranken
- Scanner
- Trittmatten
Roboteranlage Schleifscheibenkontrolle
Reishauer stand vor der Herausforderung, die Qualität und die Effizienz des Kontrollprozesses zu optimieren. Ein zentrales Anliegen war es, dass die Seriennummer auf der Schleifscheibe automatisch erkannt und mit dem System abgeglichen werden kann. Die manuelle Eingabe der Seriennummer erwies sich als zeitaufwendig und anfällig für Fehler.
Die Schleifscheiben wurden bis anhin manuell auf Paletten zur Prüfzelle geführt. Von dort wurden sie entnommen und die auf der Stirnfläche eingravierten oder aufgedruckten Nummern dem System mitgeteilt. Da die Schleifscheiben sehr schwer sind, führte dies zu hohen physischen Belastungen der Mitarbeitenden.
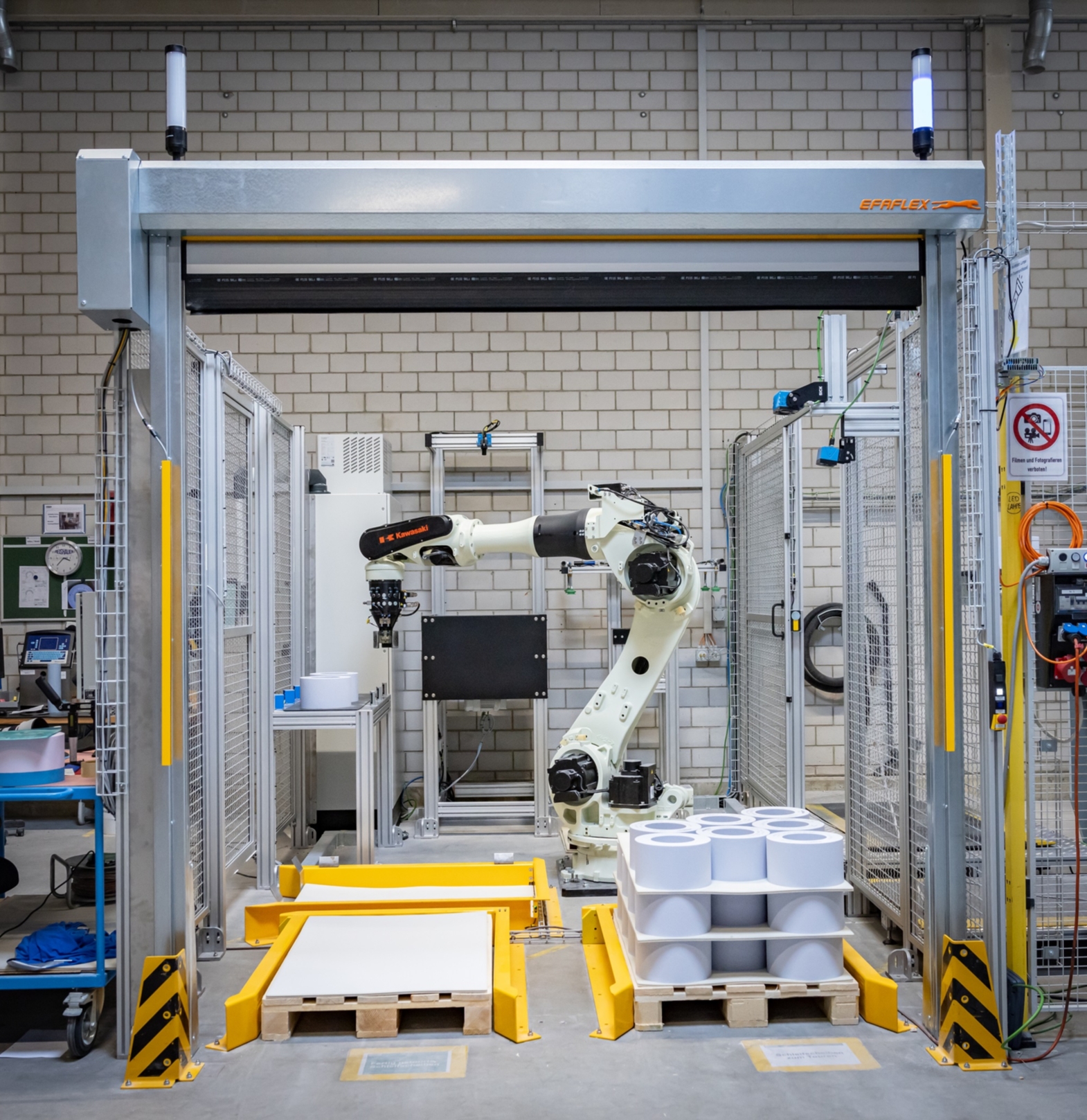
Die Herausforderung
An die bestehende Prüfzelle wird eine Palettierroboter-Anlage (KaiRoPal) gebaut. Durch das offene Tor wird eine Palette ungeprüfter Schleifscheiben und eine Leerpalette der Anlage zugeführt. Daraufhin schliesst sich das Tor und die Anlage nimmt den Betrieb auf.
Der Roboter fährt über die Palette und sucht sich mittels 3D-Kamera auf der obersten Ebene eine Schleifscheibe. Hat er diese und deren Öffnung erkannt, greift er in die Öffnung und entnimmt sie.
Der Roboter legt die Schleifscheibe in die Kamerastation. Mittels Drehteller kann die ganze Mantelfläche von der Kamera nach der benötigten Auftragsnummer, welche auf dem Werkstück eingelasert oder aufgedruckt ist, suchen. Zur Nachverfolgung des Prüfprozesses wird die gefundene Nummer mit dem übergeordneten System auf Richtigkeit gegengeprüft.
Die Schleifscheiben mit den gelaserten Auftragsnummern können mit herkömmlicher Bildverarbeitung nicht zuverlässig gelesen werden, da sich die Ziffern farblich nicht von der Scheibe abgrenzen. Deshalb wurde hier auf eine spezielle Bildaufnahmetechnik gesetzt. Diese verrichtet ihren Dienst äusserst zuverlässig.
Ist der Leseprozess mit dem Kamerasystem abgeschlossen, legt der Roboter die Schleifscheibe in eine Zentriervorrichtung der Prüfmaschine. Nach der Prüfung entnimmt er sie wieder von dort und stapelt sie auf die Leerpalette.
Wenn nötig, wird nach einer Lage Schleifscheiben eine mit Schaumstoff beschichtete Kartonzwischenlage vom Roboter aufgelegt. Dafür ist ein Greiferwechsel nötig.
Ist das Palettierbild komplett, so wird dies dem Mitarbeiter visuell angezeigt und er kann die Palette aus der Zelle herausnehmen.
Für die gesamte Palettierroboter-Anlage haben wir eine Simulation, einen Digital Twin, erstellt.
Die Lösung
Durch die Implementierung der neuen Palettierroboter-Anlage konnte Reishauer den Kontrollprozess für die Schleifscheiben erheblich verbessern und vereinfachen. Die automatisierte Inspektion reduzierte die Fehlerquote.
Die Mitarbeitenden von Reishauer profitierten ebenfalls von der neuen Technologie, da die Belastung durch die manuellen Inspektionen reduziert wurde und sie sich auf anspruchsvollere Aufgaben konzentrieren konnten.





Reishauer stand vor der Herausforderung, die Qualität und die Effizienz des Kontrollprozesses zu optimieren. Ein zentrales Anliegen war es, dass die Seriennummer auf der Schleifscheibe automatisch erkannt und mit dem System abgeglichen werden kann. Die manuelle Eingabe der Seriennummer erwies sich als zeitaufwendig und anfällig für Fehler. Die Schleifscheiben wurden bis anhin manuell auf Paletten zur Prüfzelle geführt. Von dort wurden sie entnommen und die auf der Stirnfläche eingravierten oder aufgedruckten Nummern dem System mitgeteilt. Da die Schleifscheiben sehr schwer sind, führte dies zu hohen physischen Belastungen der Mitarbeitenden.